Sulfuric Acid and Sulfur Dioxide
NORAM provides innovative process technology, engineering and equipment to metallurgical, sulfur-burning, and acid regeneration sulfuric acid plants, and sulfur dioxide plants.
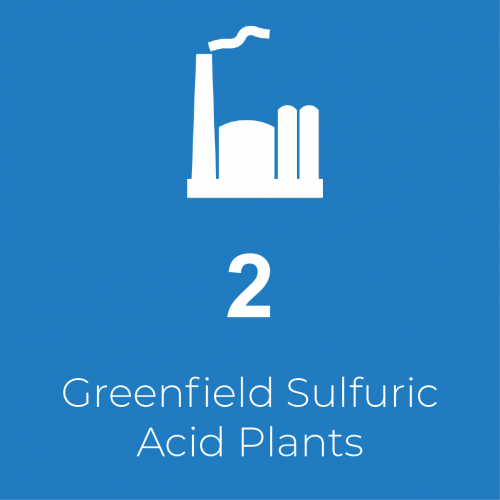
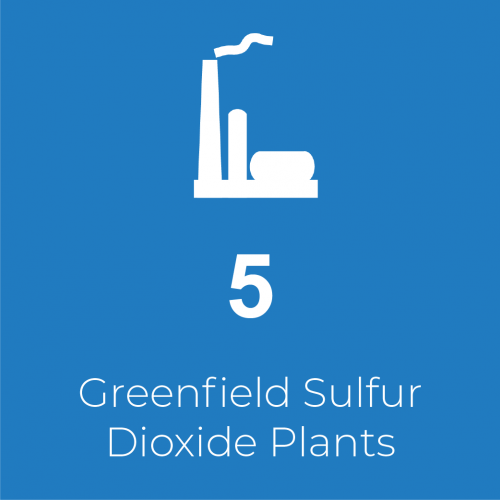
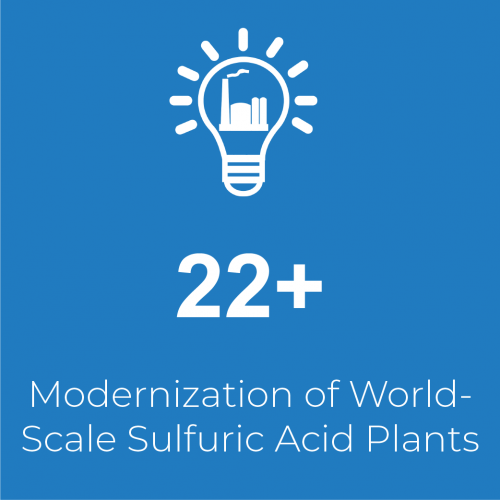
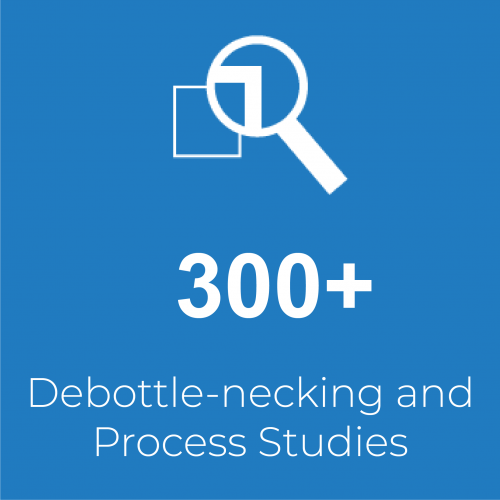
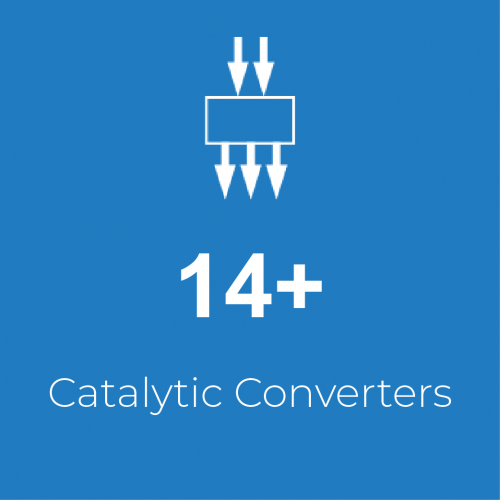
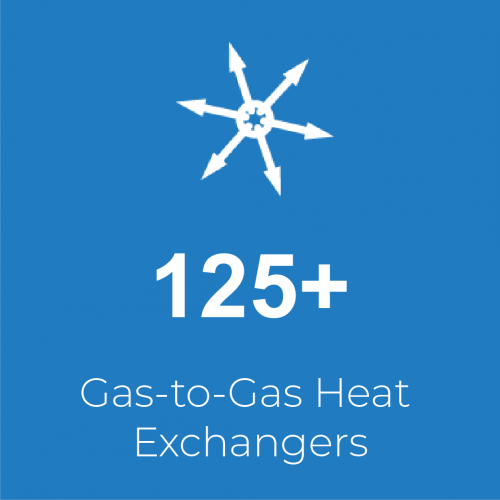
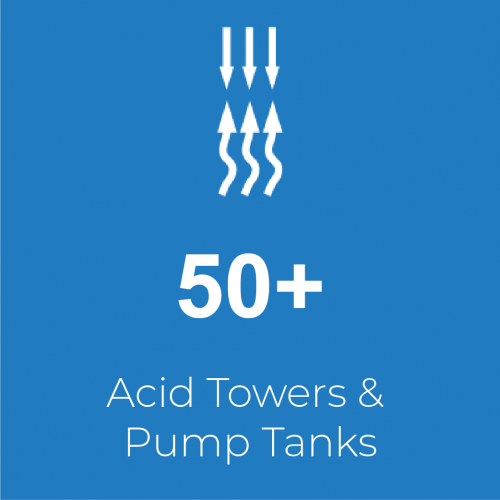
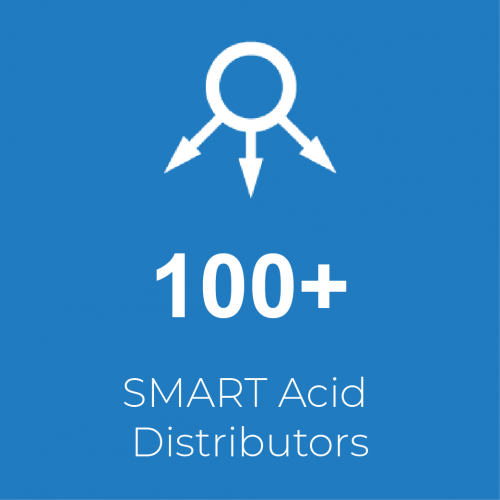
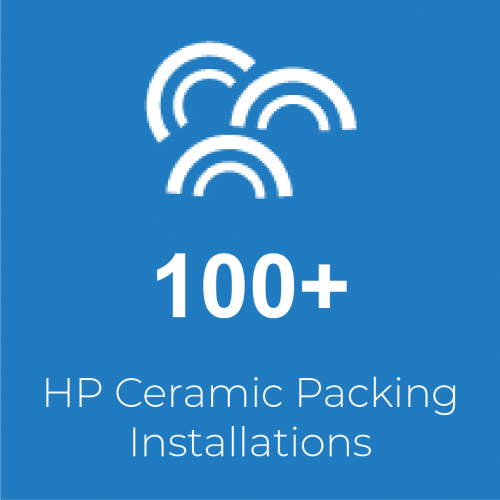
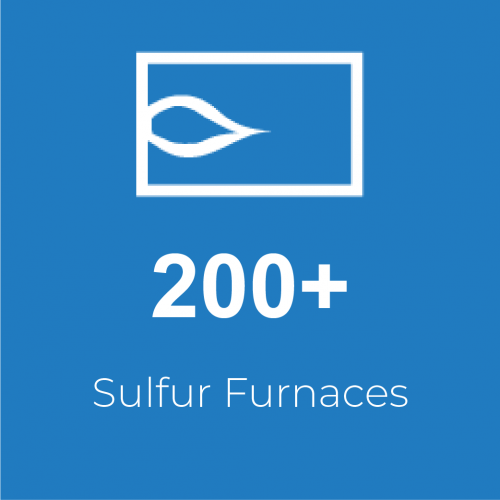
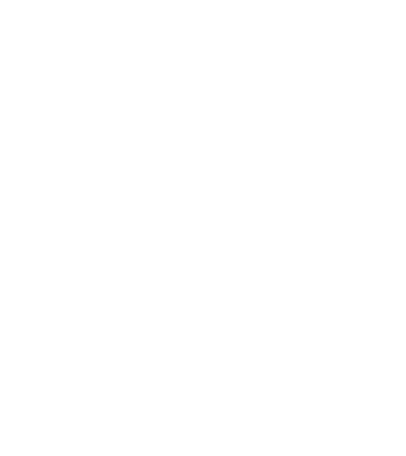
Greenfield Sulfuric Acid Plants
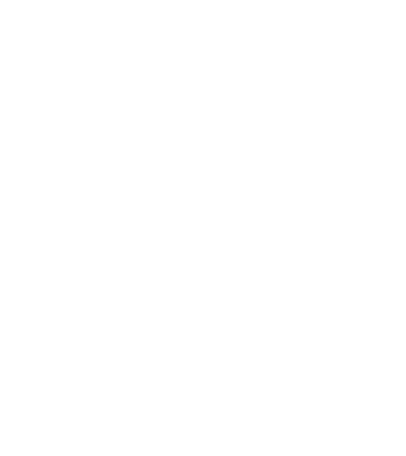
Greenfield Sulfur Dioxide Plants
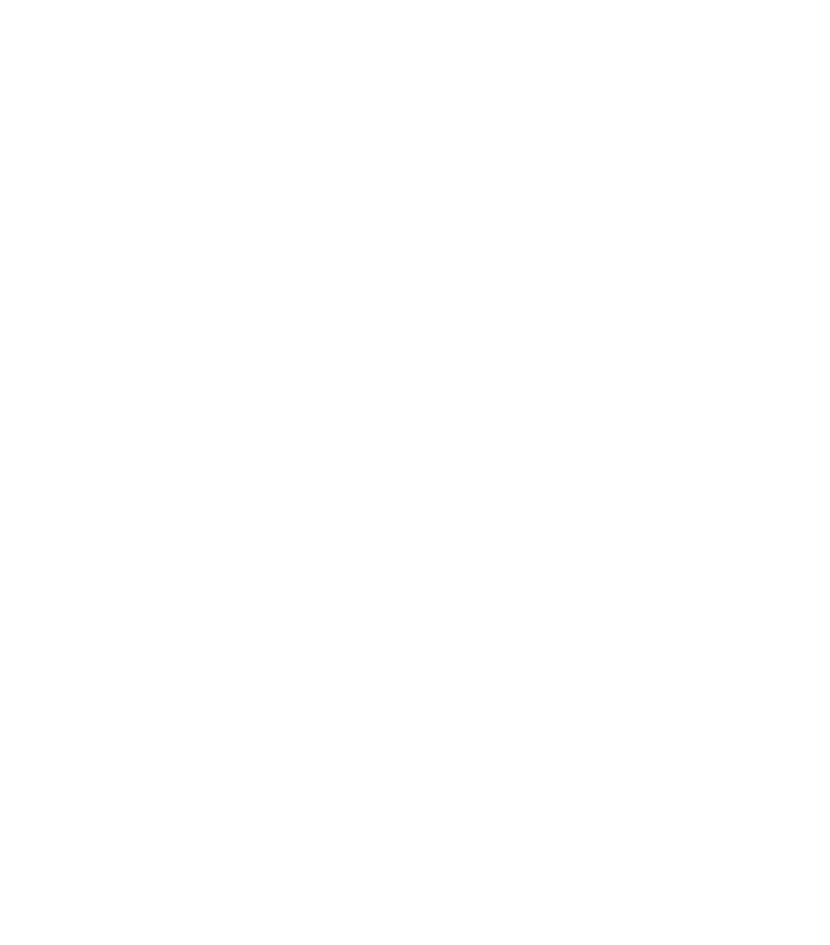
Modernization of World-Scale Sulfuric Acid Plants
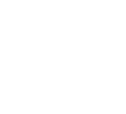
Debottle-necking and Process Studies
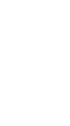
Cataytic Converters
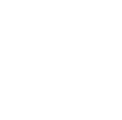
Gas-to-Gas Heat Exchangers
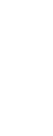
Acid Towers &
Pump Tanks
Pump Tanks
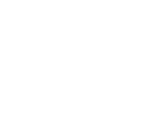
SMART Acid Distributors

HP Ceramic Packing Installations
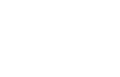
Sulfur Furnaces
NORAM’s equipment and systems, reduce environmental emissions, increase energy efficiency , increase capacity and improve plant reliability of plants of all scales around the world.
NORAM'S Sulfuric Acid and Sulfur Dioxide Plant
NORAM Engineering specializes in all aspects of sulfuric acid and sulfur dioxide manufacture. Technologies pioneered by NORAM have enabled sulfuric acid and sulfur dioxide producers around the globe to:
- Extend the life of existing facilities
- Improve operating economics and cost-effectively
- Meet more stringent environmental emission standards.
Our capabilities encompass plant design, systems design, optimization and debottlenecking studies, supply of equipment, and design and engineering of integrated plants.
We design and supply all major equipment required in a sulfuric acid and sulfur dioxide plant. Projects often start with engineering studies using proprietary process flowsheeting programs to simulate complete plants, specify new equipment or identify plant bottlenecks. Further work develops detailed designs and mechanical drawings for systems and equipment to meet stringent process specifications and reliability requirements.
Calculators
Isocorrosion Curve
Engineering, Design and Supply of Plants and Systems
NORAM studies existing facilities to identify practical methods to achieve capacity increase. NORAM specializes in complex retrofits due to a wide experience in plant upgrades. These capacity increase projects may require replacing or upgrading equipment and internals in a single stage or multiple stages of project execution.
Download Acid Plant Upgrade and Debottlenecking Studies Brochure
Equipment in sulfuric acid is replaced by state-of-the art NORAM equipment utilizing improved mechanical designs and more robust materials of construction.
NORAM’s technology is largely used for production of sulfuric acid, and oleum in sulfur-burning, metallurgical and acid regeneration facilities. The plants are also used for abatement of sulfur-containing gases at industrial scale, such as in metallurgical plants (abatement of metallurgical SO2) and pulp and paper plants (abatement of NCGs).
NORAM’s technology is used for production of SO2 gas at any industrial scale. Applications are found in industries such as pulp and paper, mining (cyanide detoxification, leaching), pulp and paper (feed to chlorine dioxide generators, sulfite and bisulfite solutions, SO2-water solutions for pulp souring), water treatment (waste water de-chlorination, bromine removal), food (de-colourization, corn wet milling), and chemicals (sulfuric acid production, in-house production of SO2, production of liquefied SO2).
Clients often approach NORAM to explore how to reduce the stack SO2 emissions on a continuous basis. NORAM’s system may include a 3 to 5 bed catalytic converter, equipment for improved gas temperature management, and SO2 conversion catalysts.
NORAM offers proprietary technology to greatly reduce the plant start-up emissions. This technology is especially suitable for adjacent acid plants, allowing for faster start-ups and ultra-low gas emissions during the plant preheat and start-up.
NORAM offers complete preheating systems to increase the temperature of process gas and equipment during start-up and process upsets. Such systems include a hydrocarbon combustion furnace and a preheat gas exchanger to achieve faster start-ups and higher reliability.
NORAM’s staff can deliver training to operators and engineers, andioning and start-up of equipment and system provide site advisory services for inspection, construction, commission.
Proprietary Equipment
Constructed from all-welded stainless steel (Typically SS-304H), which largely eliminates corrosion, while reducing maintenance requirements and extending service life. Robust mechanical designs eliminate thermal expansion and reliability issues, provide excellent gas distribution, and maximise SO2 conversion. Typical converter options include:
- Converter with internal heat exchanger: Can accommodate the hot gas exchanger integrally to simplify ducting and plant layout.
- Converter with internal welded posts: 100% of the available cross sectional area is available; multiple dished plates for improved reliability.
- Converter with single dish plate: For vessels up to medium-size, catalyst requirements can be accommodated without internal posts.
Efficient gas exchanger designs with improved heat transfer performance and high reliability include:
- RF™ (Radial Flow) exchangers: The radial geometry achieves uniformly distributed gas flow perpendicular to the exchanger tube banks, and optimized use of all heat transfer surfaces. These exchangers can be used in any position in the sulfuric acid plant.
- SF™ (Split Flow) exchangers: The SF™ Split Flow option of the RF™ heat exchanger allows effective control of the tube and tubesheet temperatures at the cold or hot end of the exchanger, to mitigate condensation and/or thermal stresses.
- NORAM-Cellchem™ sulfur furnaces: Proven in over 180 reference installations. The burners utilize air-atomization, with capacities typically ranging from 0.5 to 400 MTPD sulfur burned (1.5 to 1,200 MTPD of H2SO4 equivalent), and produce SO2 gas concentrations up to 19%. Turndown to 8 to 12.5% capacity is possible. Two configurations are offered:
- CF (Cyclone-flame): For very small scale (0.5 to 16 MTPD sulfur burned).
- SF (Spiral-flame): For medium scale (5 to 400 MTPD sulfur burned).
- Pressure atomization sulfur furnaces: For larger plants producing 100 MTPD to 3,000+ MTPD of H2SO4 equivalent capacity.
- Preheat furnaces: For plant preheating applications.
- Spent acid regeneration furnaces: For decomposition of spent sulfuric acid. Feed from a variety of sulfur-containing streams are viable, including H2S, spent acid, sulfur as well as hydrocarbons.
Acid tower designs are available for Drying, Interpass Absorption, Final Absorption, Oleum, Quench, Stripping and Scrubbing. Design options are:
- Brick-lined towers: Brick lining has traditionally been used in acid towers, as it withstands the widest possible range of acid concentrations should upset conditions occur. We offer state-of-the-art bricking, with innovative stable dished bottoms, self-supporting dome packing support, and internal or external dilution.
- Alloy towers: Fabricated in high-silicon stainless steel (NORAM SX®, UNS 23615). The use if this alloy allows for lighter equipment and faster installation, often critical in plant retrofits.
Vertical-type and bullet-type configurations are offered for service in strong acid circuits. Brick-lined or NORAM SX® materials of construction are available. Tanks can be operated with or without internal dilution.
- SMART™ acid distributors: Allows for easy installation, and cleaning from external ports without entering the tower. Uniform acid distribution throughout tower cross section area, low spray generation rate is also achieved.
- Trough acid distributors: A robust design with all-metal construction.
Download SMART Acid Distributors Brochure
Our proprietary HP™ packing is made through a slip-casting process which produces saddles of uniform shape within a narrow range of size tolerances. The high-performance design achieves high absorption capacity and low pressure drop. Breakage during shipping and installation has typically been less than 0.1 percent. NORAM HP™ packing is often used to debottleneck acid towers and achieve higher plant capacities due to pressure drop savings.
- Anodically protected acid coolers: Use large diameter cathodes, which minimize the voltage drop along the cathode and give more uniform passivation.
- NORAM SX® alloy acid coolers: Often preferred for simpler installation and virtually maintenance-free operation. NORAM SX® coolers can deal with higher temperatures and can be used for boiler-feed water preheating.
- Alloy acid coolers for seawater service: Coolers are offered in alloy materials without anodic protection for high-chloride service
NORAM provides systems for internal acid dilution using weak acid or water. These systems can be located inside towers and pumptanks, or be configured externally.
We inventory a comprehensive selection of metal plate, flanges and piping for hot sulfuric acid service. Training for welding of NORAM SX® material is also offered.
Developed from NORAM SX® for corrosion resistance, designs include:
- A family of butterfly-type valves, triple offset triple offset, Class V valves, designed for use in both control and tight shut-off applications, available in a variety of sizes and configurations.
- Ball-type valves
Capture of entrained H2SO4 droplets and mist can be addressed by:
- Cyclonic capture: Applicable downstream of acid towers to reduce acid carryover and to protect equipment, using cyclonic principles.
- Demister vessels: Filter vessels and knock-out vessels fitted with conventional meshpads, impaction candles or Brownian diffusion candles.
Manufactured from NORAM SX® alloy. The strainers can be located inside acid towers, at pump suction, or be configured externally with internal removable basket.
Our experience with thermal expansion and thermal cycling allows robust gas ducting and systems to be designed. We incorporate finite element analysis (FEA) and special expansion joint designs suitable for high temperature gas service into our designs.